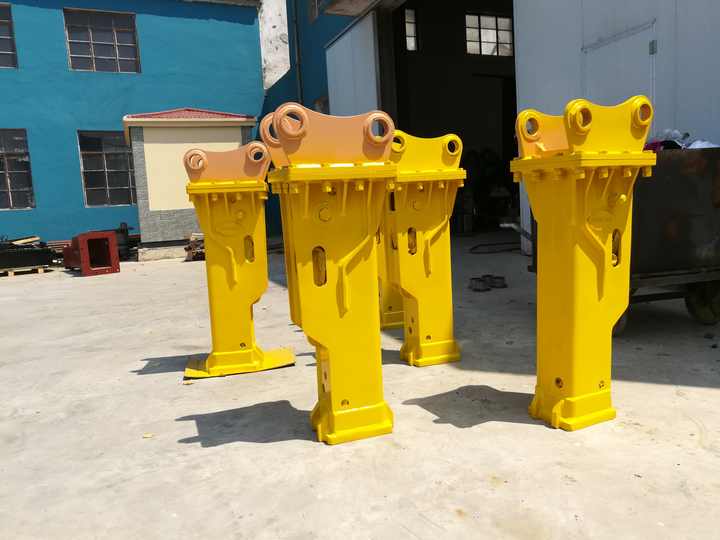
For professionals in construction and demolition, understanding how a demolition hammer works is essential for optimal usage and equipment selection. This article explains the mechanics behind demolition hammers, breaking down the process into key components and steps to help engineering and construction personnel maximize the effectiveness of this powerful tool.
Introduction to Demolition Hammer Mechanics
A demolition hammer is a high-powered tool that breaks down materials like concrete, asphalt, and rocks through high-impact force. Unlike regular hammers or drills, which rely on rotating motion, demolition hammers use a reciprocating (back-and-forth) motion powered by hydraulic, pneumatic, or electric systems to generate force. This targeted impact makes demolition hammers ideal for construction sites where controlled destruction of hard surfaces is required.
Working Mechanism of a Demolition Hammer
The operational process of a demolition hammer includes several key stages, each of which contributes to its effectiveness and durability.
1. Power Generation
- Hydraulic-powered hammers use the excavator’s hydraulic system to convert hydraulic pressure into mechanical energy.
- Pneumatic hammers rely on compressed air to generate power.
- Electric hammers are commonly smaller and portable, using electric power to move the internal piston.
Diagram 1: Power Generation Mechanism in Hydraulic and Pneumatic Hammers
2. Piston Movement and Impact Force
Once powered, the hammer’s internal piston reciprocates, creating a striking motion. Here’s how it works in a hydraulic hammer:
- Hydraulic Fluid Movement: Pressurized fluid enters the hammer cylinder, pushing the piston forward.
- Striking Action: The piston strikes the chisel or bit at the front of the hammer, generating high-impact force.
This movement repeats continuously, delivering consistent, rapid blows to the target material.
Diagram 2: Piston Motion and Striking Action in a Demolition Hammer
3. Tool Attachment and Impact Transfer
At the hammer’s front end, a chisel or tool attachment transfers the impact energy to the material. The impact frequency and force depend on the piston’s speed and the hydraulic system’s pressure.
- Chisel Types: There are various types of chisels, including moil, blunt, and pointed. Each is selected based on the material being broken.
- Material Transfer Efficiency: The chisel material, usually made of hardened steel, is critical to maximize energy transfer and durability.
4. Vibration Absorption and Heat Management
Demolition hammers experience significant vibration and heat generation during operation. Therefore, the design includes:
- Shock Absorbers: Reduce vibrations felt by the operator.
- Cooling Systems: Hydraulic hammers use the excavator’s cooling system to manage fluid temperature, preventing overheating.
5. Exhaust and Recirculation
In hydraulic and pneumatic systems, exhausted air or fluid is recirculated to maintain efficiency. This system minimizes energy loss and reduces fuel consumption.
Benefits of Understanding Demolition Hammer Mechanics
- Enhanced Productivity: Knowing how the hammer works helps operators select the right tool and adjust settings for faster results.
- Reduced Wear and Tear: Correct usage minimizes equipment strain and prolongs tool life.
- Improved Safety: Understanding internal mechanics promotes safer handling and operation.
Comparison of Demolition Hammer Power Sources
Power Source | Pros | Cons |
---|---|---|
Hydraulic | High power, compatible with excavators | Requires hydraulic system maintenance |
Pneumatic | Consistent power, suitable for indoors | Requires an air compressor |
Electric | Portable, easy to use | Lower power, suitable for small jobs only |
Table 1: Comparison of Demolition Hammer Power Sources
Applications of Demolition Hammers
Demolition hammers are used in various applications depending on the type of power and chisel attachment. Common uses include:
- Concrete and Road Demolition: Ideal for breaking up concrete slabs, asphalt, and pavement.
- Building Demolition: Controlled breakdown of walls and structural elements in renovation projects.
- Mining and Quarrying: Breaking up rocks and other materials in extraction sites.
- Landscaping and Trenching: Removing rocks, roots, and other obstacles from soil during land preparation.
Diagram 3: Application Scenarios for Demolition Hammers
Frequently Asked Questions (FAQ)
Q: What type of power source is best for heavy-duty demolition?
A: Hydraulic-powered hammers are the best for high-demand jobs, as they offer consistent power and can handle prolonged use with minimal downtime.
Q: How often should I maintain a hydraulic demolition hammer?
A: Regular maintenance is crucial. Check hydraulic fluid levels daily and inspect seals and connections monthly to avoid potential leaks or performance loss.
Q: Can I use the same chisel for concrete and asphalt?
A: It’s best to select a chisel type based on the material. For instance, blunt chisels work well for concrete, while moil points are suited for asphalt.
Conclusion
Understanding how a demolition hammer works is essential for selecting the right equipment and ensuring its efficient, safe operation on the job. By breaking down the working principles and components, construction professionals can make informed decisions on chisel types, power sources, and maintenance requirements to get the best performance and lifespan from their demolition hammer. For further details on the right model for your excavator and project needs, contact us today.